2020
Direkwatana, Chawaphol; Suthakorn, Jackrit
Design of High Performance DC Motor Actuated Cable Driving System for Compact Devices Journal Article
In: International Journal of Power Electronics and Drive Systems (IJPEDS), vol. 11, no. 2, pp. 580–593, 2020, ISSN: 2722-256X.
Abstract | Links | BibTeX | Tags: Electrical and Electronic Engineering, Energy Engineering and Power Technology
@article{Direkwatana2020b,
title = {Design of High Performance DC Motor Actuated Cable Driving System for Compact Devices},
author = {Chawaphol Direkwatana and Jackrit Suthakorn},
url = {https://bartlab.org/newweb/wp-content/uploads/2023/08/20622-39904-1-PB.pdf},
doi = {10.11591/ijpeds.v11.i2.pp580-593},
issn = {2722-256X},
year = {2020},
date = {2020-06-01},
urldate = {2020-06-01},
journal = {International Journal of Power Electronics and Drive Systems (IJPEDS)},
volume = {11},
number = {2},
pages = {580--593},
publisher = {Institute of Advanced Engineering and Science},
abstract = {The cable transmission is widely used in the remote operation or complex geometry with high stiffness and low backlash. Larger drum is required to reduce and error of transmission in long stroke. An error of the desired position occurs due to the fleet angle while cable winding on a drum. Therefore, a new cable driving module which overcomes this problem is proposed. A new cable driving module with a sliding platform is connected to the actuator unit. A motion of the sliding platform is corresponding to a screw rod connected to an actuator. The precision of the driving system is measured by a high-resolution rotatory encoder and high gear ratio actuator. Results are measured by load and error of the system. A load of system shows a performance of overall translation and rotation of the drum at different speeds. An error of the system is measured from forward and reverse direction by increasing and decreasing the number of turns with constant speed. A system has an average load consumption along a long stroke of cable winding which has no significant problem on the screw platform. Multiple turns have low error value in specific and continuous turn in forward and reverse motion. A new cable driving system is proved in precision movement. The fleet angle is eliminated in new mechanism. Along with a constraint motion, there is no significant change in load consumption. An error is low value in a different direction of movement. Hence, a new design of cable transmission can perform in high performance and small size of the system.},
keywords = {Electrical and Electronic Engineering, Energy Engineering and Power Technology},
pubstate = {published},
tppubtype = {article}
}
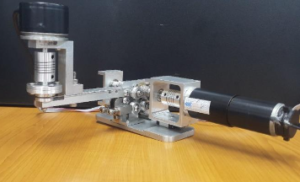
2019
Pillai, Branesh M; Suthakorn, Jackrit
Motion Control Applications: Observer Based DC Motor Parameters Estimation for Novices Journal Article
In: International Journal of Power Electronics and Drive Systems (IJPEDS), vol. 10, no. 1, pp. 195–210, 2019, ISSN: 2088-8694.
Abstract | Links | BibTeX | Tags: Electrical and Electronic Engineering, Energy Engineering and Power Technology
@article{Pillai2019b,
title = {Motion Control Applications: Observer Based DC Motor Parameters Estimation for Novices},
author = {Branesh M Pillai and Jackrit Suthakorn},
url = {http://bartlab.org/newweb/wp-content/uploads/2023/06/15.pdf},
doi = {10.11591/ijpeds.v10.i1.pp195-210},
issn = {2088-8694},
year = {2019},
date = {2019-03-01},
urldate = {2019-03-01},
journal = {International Journal of Power Electronics and Drive Systems (IJPEDS)},
volume = {10},
number = {1},
pages = {195--210},
publisher = {Institute of Advanced Engineering and Science},
abstract = {Estimation of motor inertia and friction components is a complex and challenging task in motion control applications where small size DC motors (<100W) are used for precise control. It is essential to estimate the accurate friction components and motor inertia, because the parameters provided by the manufacturer are not always accurate. This research proposes a Sensorless method of determining DC motor parameters, including moment of inertia, torque coefficient and frictional components using the Disturbance Observer (DOB) as a torque sensor. The constant velocity motion test and a novel Reverse Motion Acceleration test were conducted to estimate frictional components and moment of inertia of the motor. The validity of the proposed novel method was verified by experimental results and compared with conventional acceleration and deceleration motion tests. Experiments have been carried out to show the effectiveness and viability of the estimated parameters using a Reaction Torque Observer (RTOB) based friction compensation method.},
keywords = {Electrical and Electronic Engineering, Energy Engineering and Power Technology},
pubstate = {published},
tppubtype = {article}
}
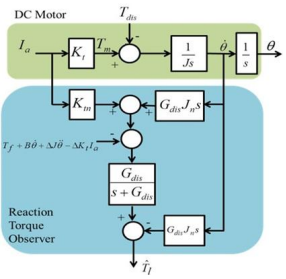